

They make it so easy to be sure it’s calibrated now after disassembling the printer. The printing results are now much better, and I’m no longer forced to use rafters.Ī big thanks to wbvreeuwijk for making the calibration brackets. Its build volume is perfect for printing a wide variety of objects, and its pre-calibrated build plate ensures accurate prints every time. I could make it even better, but it is close enough for me. So now I have a difference of 0.1 instead of 2.0 when calibrating. While continuing to hold it in place, I tightened the screws. Using the supplied hex wrench, I loosened the screws while holding down the arm so that both the printed alignment stands where touching the print bed. The first leftmost screws are for holding a plastic bracket, but the next two are the ones you need to loosen to be able to adjust the Y-axis. Instead of removing the whole arm, I just used a screwdriver to pry out the size of the axis closest to the Z-arm. Just make sure to use a pen to mark the exact location of the arm to be able to assemble it as it was before. So I turned the printer around and removed the three screws that hold the Y-axis rails to the Z-axis tower. They fit snuggly on the Y-axis linear rails.Īfter checking, I noticed the 2mm gap on the right side of the alignment stands.
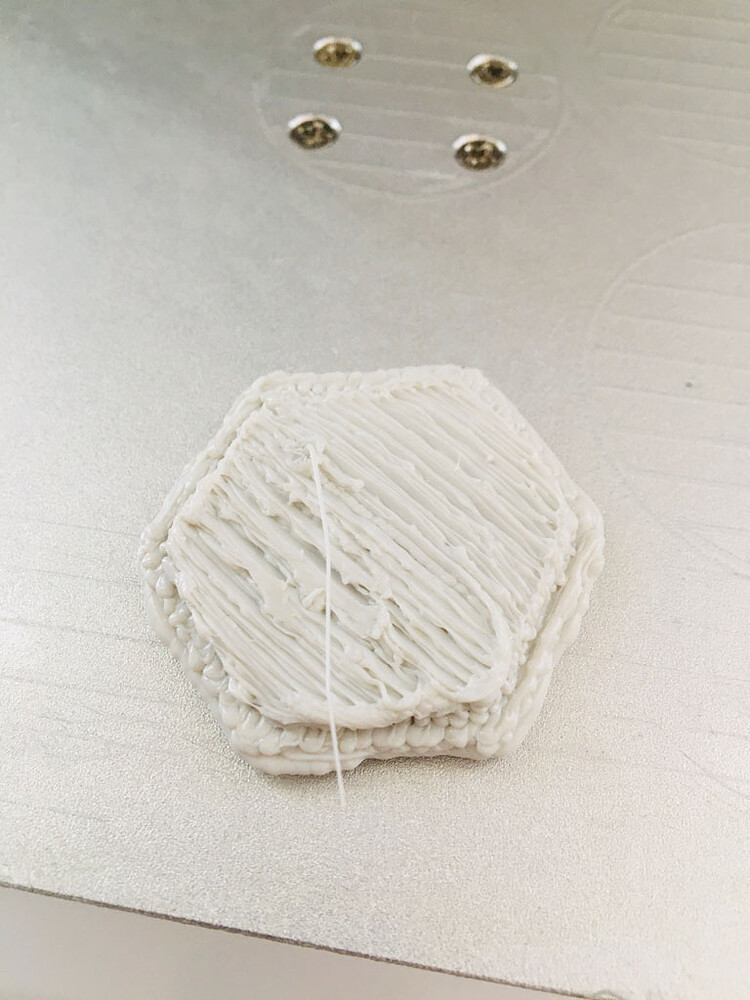
I just needed to move the print plate to the center and attach the calibration arms to the axis after removing the print head. I found a stand on Thingiverse, so I printed two of them. In App function allows user to check and calibrate the angle of vertical features to platform, making sure the perpendicularity. But I finally found an easy way of fixing the Y-axis adjustment. There is a calibration feature inside the program, but you need to always print with a raft to get your prints level, with the accompanied wastage of PLA plastic. We have since released the Slap Mat for resin printing.
Calibrating cetus3d install#
Our first product line, the Wham Bam Flexible Build System, addresses the need for printers to have a more reliable build surface which is easy to install and makes printing and removing a breeze. If I zeroed out the nozzle on the left side, the right side was 2.0 lower. Wham Bam Systems is dedicated to improving the 3D printing experience through innovation. Unfortunately, the calibration quality from the factory was terrible, which is unfortunate on such a superb printer. It’s a cheap printer for around $300, but it has linear rails and can give excellent results. This can be solved by adding spacer sticker to X or Y motor (side face linear bearing) or slightly turn the screws on top of the Z-axis.I’ve been busy the last couple of weeks, learning all the ins and outs of my new Cetus3D 3D-printer. Therefore after some use of the axis may have some slight dimensional change which result in the endpoint not able to be detected. However this mechanism is not continuous all along the axis, but the sensitive region is intermittent. This innovative mechanism take advantage of the waveform change of electric current during the stalling of motor when the axis endpoint is reached. MK2 machines use a complete different method. While MK1 and MK3 use limit switch for homing trigger. We can do this by printing a single perimeter cube and adjusting the extrusion multiplier so that the width of the walls is the same as.
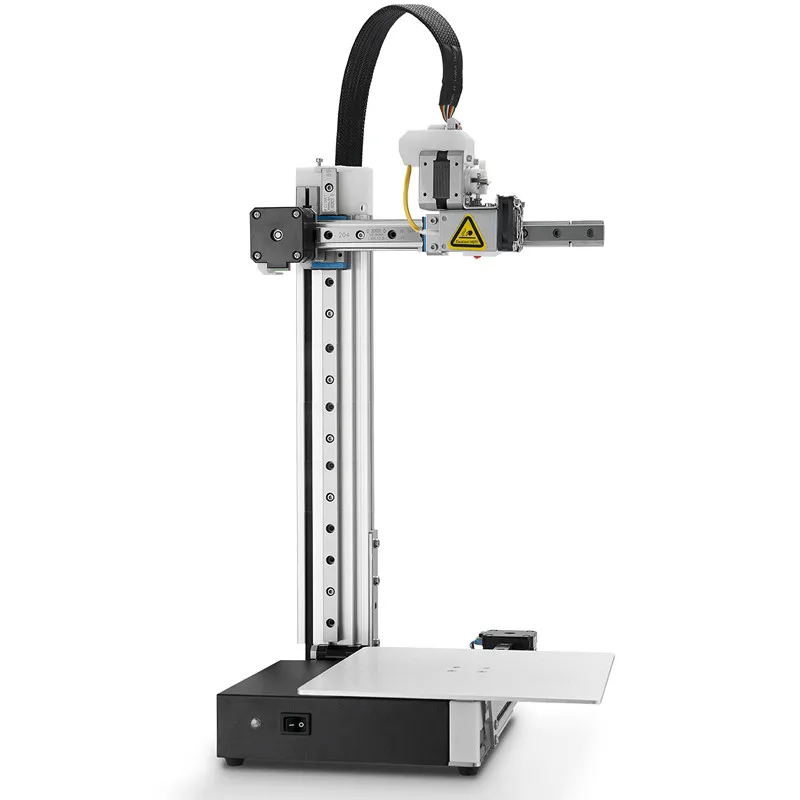
You can solve the problem by adjusting the adjustment screw on top of the Z axis by turning it for 1/4 turn on either direction.įor X and Y axes, you can use the stickers included in the package to calibrate the homing. Now that we know the right amount of filament is being fed into the hotend by the extruder mechanism, we can further calibrate based on how the plastic flows from the nozzle. This is caused by slight dimensional change of the machine's axis. The result is continuous search of homing point of the axis, which is chattering of the axis. The problem is due to the homing mechanism cannot be triggered. This is specific problem occur on Cetus MK2 machine, MK1 and MK3 Cetus do not have this issue.
